Max-IR Labs, a developer of infrared sensors for industrial process control and biochemical analysis, announced plans for field demonstration and testing of its ISMIRTM technology.
On Monday, Jan. 17th, Max-IR Labs, a member of the UT Dallas Venture Development Center, initiated field testing of its patented sensor technology at a local wastewater treatment plant (WWTP). The sensor evaluation follows a successful technology development work in partnership with the lab of Professor Amy Walker at The University of Texas at Dallas (UTD), under SBIR funding from the National Science Foundation (NSF).
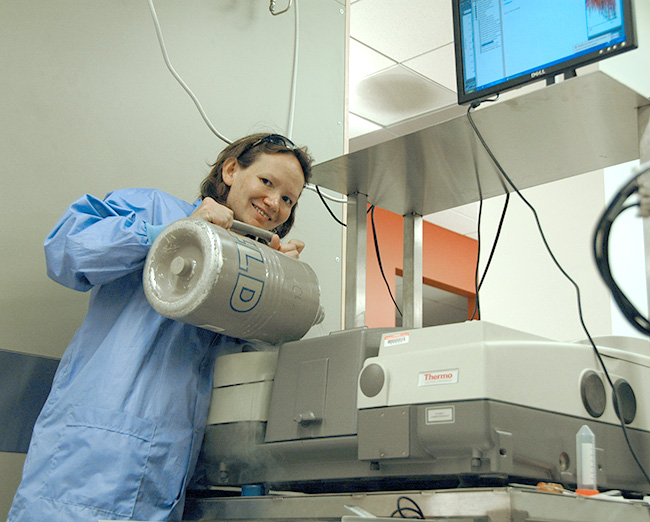
Treatment of municipal sewage is a very energy-intensive process: it accounts for over 1% of total U.S. electric energy consumption. In-line monitoring of nitrogen contaminants, such as nitrate and ammonia, at a WWTP using Max-IR’s sensor can enable automated controls and optimization of the wastewater treatment process, resulting in significant energy savings. Municipal sewage is treated in industrial-scale bioreactors, where the metabolic activities of various microorganisms are used for biodegradation of the nitrogen contaminants into N2 gas. This treatment requires aeration – a process in which air is passed through the treated wastewater. Aeration represents over 50% of the WWTP electric power consumption. However, implementation of real-time controls based on in-line sensors can reduce energy consumption due to aeration by as much as 20%.
Max-IR Labs’ sensor technology is based on pre-concentration of contaminants using ion-selective materials, and subsequent infrared (IR) spectroscopy for detection of the nitrogen-based contaminants. If implemented across all municipal WWTPs in the U.S., energy savings would equate to a reduction of roughly 2M metric tons of CO2 per year from reduced electric power generation/usage. This is roughly equivalent to CO2 reduction from converting 900,000 cars from gasoline to electric, or about the number of Tesla cars sold in 2021. Potential energy savings and greenhouse gas reduction from implementation of Max-IR’s technology on a global scale would be much larger.
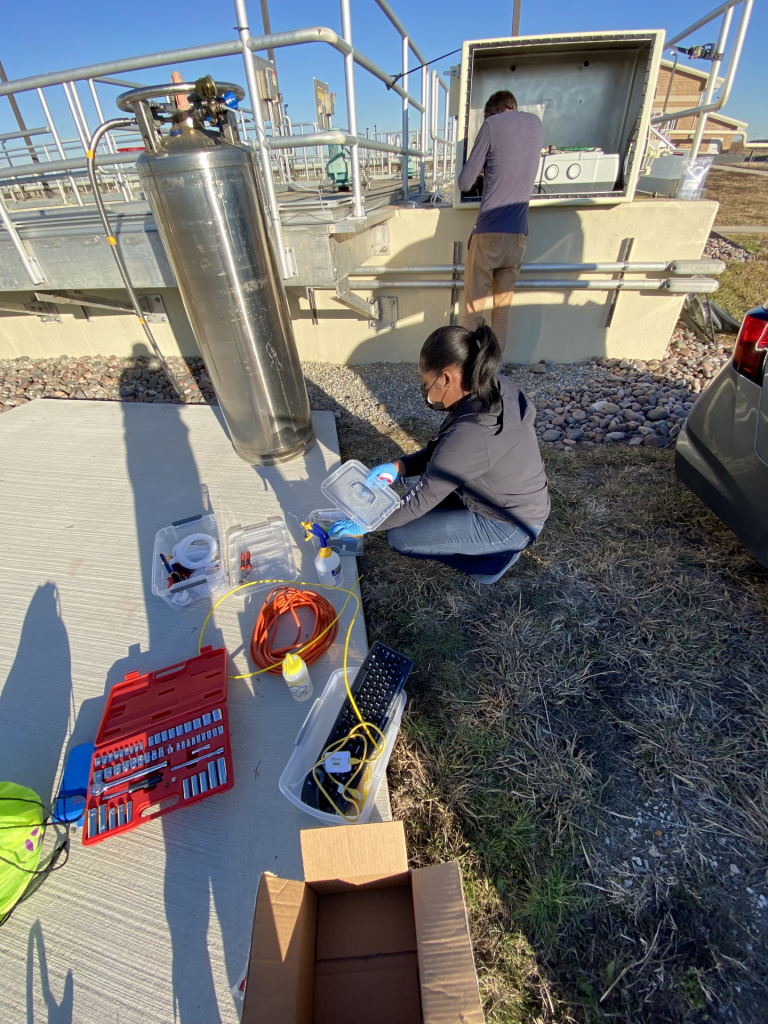
“Sensor evaluation at the wastewater treatment plant is an important milestone for our startup. It will prove that the technology works in harsh field conditions. This demonstration opens up new possibilities for collaborations and commercialization activities with the key stakeholders in the analytical instrumentation and environmental sensing marketplace,”said Dr. Roodenko, founder and CEO of Max-IR Labs. Beyond detection of nitrogen compounds at WWTPs, Max-IR Labs’ sensors can be utilized to control processes in other industrial and lab-scale bioreactors.
Methods developed by Max-IR Labs for analysis of environmental water has led to new R&D efforts focused on detection of harmful perfluoroalkyl substances (PFAS), as well as toxic industrial materials (TICs) and toxic industrial chemicals (TIMs) in water. Max-IR Labs won a Phase I ARMY STTR for development of a new methodology to screen TICs/TIMs in potable water filtration systems. The Army-sponsored Phase I project was carried out with support from UTD under a subaward to the lab of Dr. Jean-François Veyan.
You must be logged in to post a comment.